Double-Loop Feedback
In traditional industrial activity, «quality control» and «zero defects» were the watchwords. In order to shield the customer from receiving poor quality products, aggressive efforts were focused on inspection and testing at the end of the production line. The problem with this approach is that the true causes of defects are never identified, and there are always inefficiencies due to the rejection of defects. Variation is created at every step in a production process, and the causes of variation need to be identified and fixed. If this can be done, then there is a way to reduce the defects and improve product quality indefinitely. To establish such a process all business processes should be part of a system with feedback loops. The feedback data should be examined by managers to determine the causes of variation, what are the processes with significant problems, and then they can focus on fixing that subset of processes.
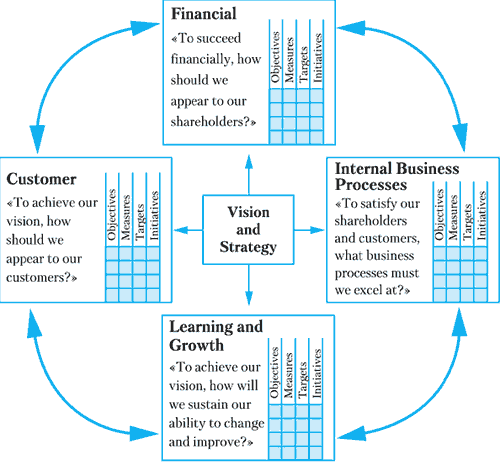
The BSC incorporates feedback around internal business process outputs, as in TQM, but also adds a feedback loop around the outcomes of business strategies. This creates a «double-loop feedback» process in the balanced scorecard.
Более 800 000 книг и аудиокниг! 📚
Получи 2 месяца Литрес Подписки в подарок и наслаждайся неограниченным чтением
ПОЛУЧИТЬ ПОДАРОКДанный текст является ознакомительным фрагментом.